| A cylindrical spur gear is easily compared to a cylindrical
friction wheel. As the latter, the former allows the transmission of a
rotational movement between two parallel shafts, the ratio of angular
velocities is determined by the ratio of the diameters of the
wheels..
How,
whereas in the case of friction wheels, which are incapable of
transmitting large forces and which, forcibly lead to a certain slippage,
in the case of gears, the liason, obtained by obstacles, makes for a true
transfer of power and can transmit considerable tork
values.
The elements making up a toothed wheel which correspond to a
friction wheel are called the pitch elements: pitch circle, cylindrical
pitch, pitch circle diameter (PCD). These elements are very difficult
to measure on a gear.
The coupling of
two wheels working together is known as a gear. When the two wheels are of
different diameters, the smaller of the two is known as a pinion, the
larger - the gear.
The drive
wheel governs the movement of the driven wheel.
A rack is
considered to be a wheel of infinite diameter (it's pitch surface is a
plane).
The
cylindrical pitch of a gear is an imaginary cylinder whose surface
form is found by meshing gears so that the surfaces actually touch each
other (in other words - it is as if you are using two friction wheels of
the same diameter). A straight section through this cylinder will give the
pitch circle, which has a diameter d(PCD).
The external
diameter is the diameter measured from the highest point on the
teeth.
The base circle
diameter is the diameter when measured from the root of the
teeth.
The face is the
portion of the surface of a tooth between the head and
root.
The Circular
Tooth Thickness is the length of the arc between the two faces of a tooth.
Taken from the PCD.
The profile is a
section through the face of the tooth. The form of this profile is known
as an INVOLUTE
CURVE.
The pitch
is the length of the arc, measured on the pitch circle, between similar
points on two consecutive teeth. It is equal to the product of and the
module.
The module
is used as a basis for all calculations of tooth dimension. This parameter
may be found easily by a mathematical formula..
In order for two
wheels to mesh they must have the same module (the same size of
tooth). Two gears of different modules will be
incompatible.
The dimensions of
a spur gear are defined by the number of teeth and it's module. All
other dimensions are linked to these two by The following
formulas:
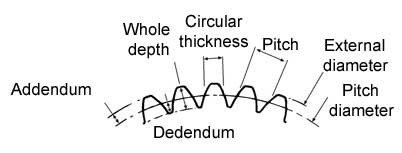
 |
STANDARD TOOTH |
Sym-bols |
Formulas |
Unit |
Module |
m |
p  |
mm |
Pitch |
p |
m x  |
mm |
PCD |
d |
Z x
m |
mm |
number of
teeth |
Z |
d m |
|
External
diameter |
D |
(Z + 2) x m |
mm |
Addendum |
ha |
m |
mm |
Dedendum
for mod. 0,25 to 1,25 |
hf |
1,40 x
m |
mm |
Dedendum
for 1,5 to 8 |
hf |
1,25 x
m |
mm |
Whole depth
for mod 0,25 ?nbsp;1,25 |
h |
2,40 x
m |
mm |
Whole depth
for mod 1,5 ?nbsp;8 |
h |
2,25 x
m |
mm |
Circular
thickness |
e |
2 m |
mm |
Consult tooth size for
gears of module 0,20 to 6.
Centre
to centre |
a dA + dB 2 |
The centre to centre distance tolerance is
0/+0.05 |
Speed
ratios |
W1 = Z2 W2 = Z1 |
W1 = Input speed W2 = Output
speed Z1 = Number of teeth on drive
wheel Z2 = Number of teeth on driven
wheel |
To
assure continuous meshing, One couple of teeth must mesh before the
previous pair seperates. In the case where there are a small number of
teeth on a gear, a correction will be necessary to avoid interference
between consecutive pairs of teeth. |
|
|
Advantages, inconveniences and advice.
- Possibility of axial displacement,
- No
axial forces,
- Reduction ratios of 2:1 to 40:1
- The
simplest of gear systems
- Gears
of the same module are interchangeable.
| How is the module calculated? |
The pitch circumference is : |
Pitch circumference = x
PCD |
| | Also |
Pitch circumference = Number of teeth x
Pitch |
| | Therefore : |
Number of teeth Z x Pitch (P) = x
PCD |
| | Therefore : |
| | |
Where P = Pitch, d = PCD and Z = Number of
teeth
| By
definition, the resultant is known as the Module (m). It can
be shown that : |
| |
Therefore
the basic formuli for gears may be found |
| d = m
Z |
| p =
m |
From a
geometric point of view, the module can be found on a tooth. It is the
distance, in mm, between the Pitch arc and the External arc. For example,
for module =2, there will be 2mm between the Pitch and External circles.
Returning to the diameters, to find the external diameter it is necessary
to add 2 x module to the PCD.
Therefore
one finds : |
d(ext) =
m Z + 2m |
| d(ext) =
m (Z+2) |
| |
What is the shape of an involute curve?
This
shape is defined by the trajectory of a point situated on a spur which
will roll, without slipping, over a circle. This form has many
advantages..
- There
is a large tolerance in the distances between the gears before the
operation of the system is affected.
- One
single tool per module, allows for the machining of all sizes of wheel,
how many teeth they have.
- The
wear on the mating surfaces of the gears is much more evenly spread than
on other profiles.
- Vibration levels are lower than other profiles.
See also
Profiles of teeth on
gears and racks
Tooth
size for gears of 0,25 to 6 module |
| |